基于热-结构耦合的盘式制动器磨损状态下制动噪声研究
1 制动噪声的产生机理
2 盘式制动器模态与不稳定系数分析理论




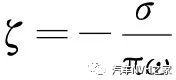
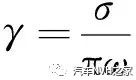
3 盘式制动器热-结构耦合模型
3.1 制动器摩擦热流密度

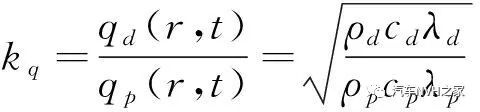
3.2 仿真模型的分析与简化
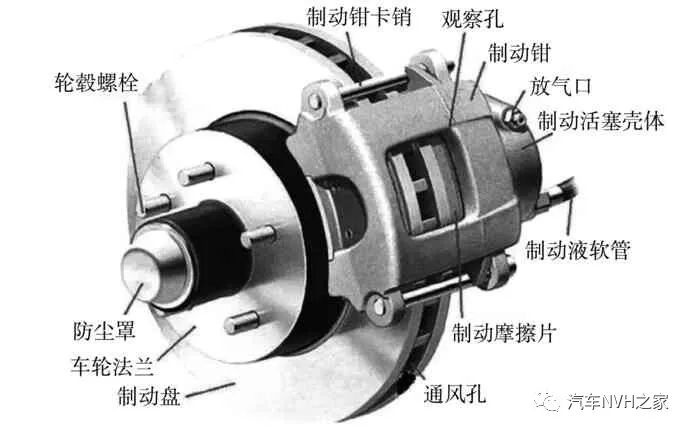

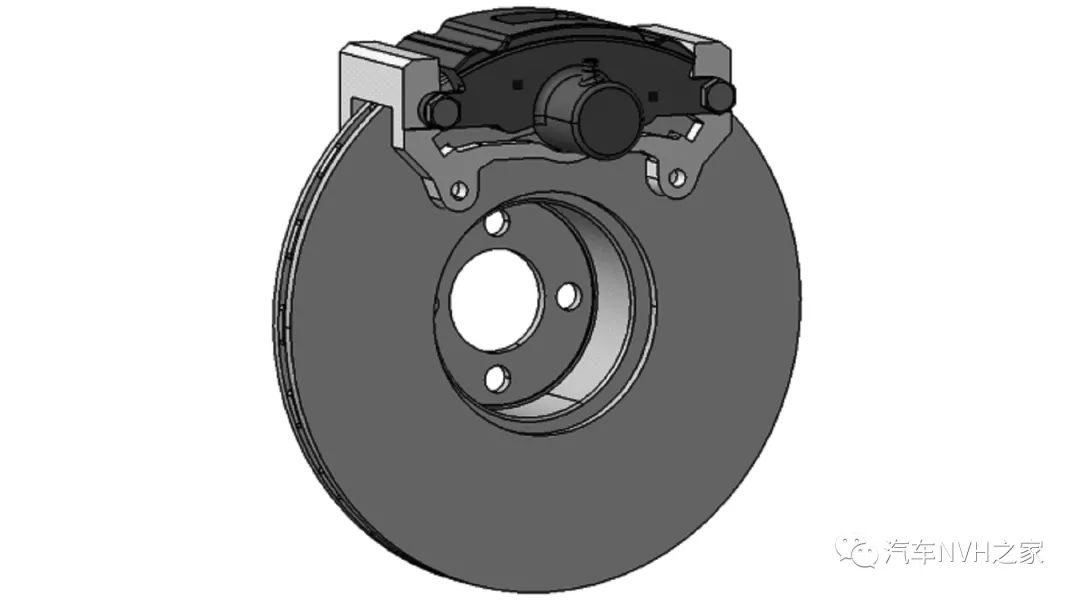

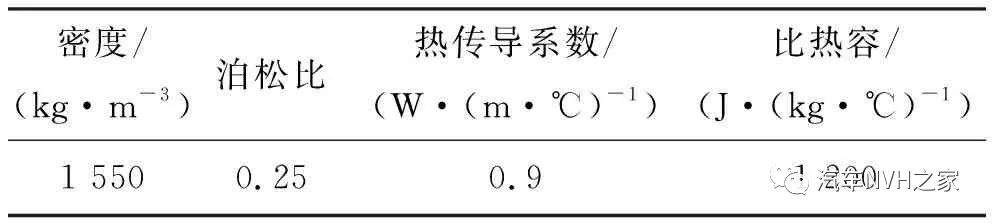
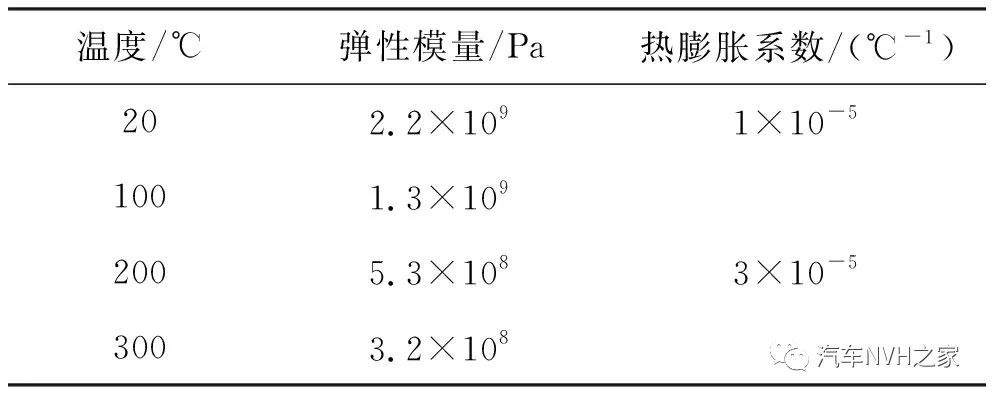
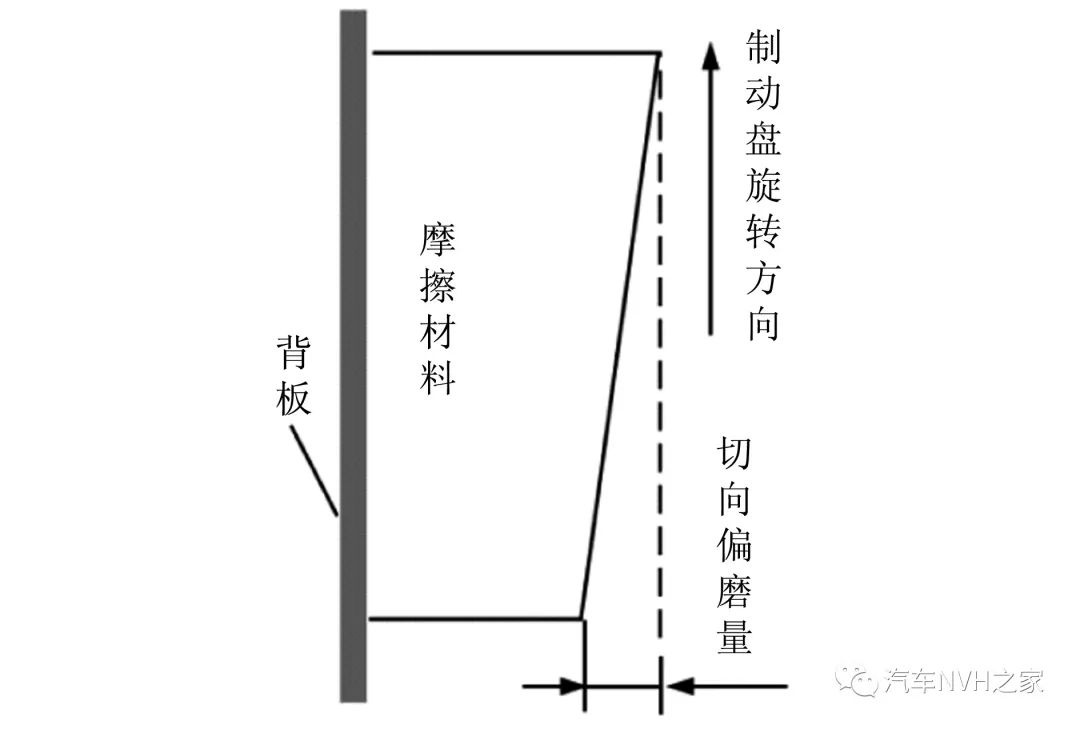

3.3 盘式制动器典型结构的建立与网格划分
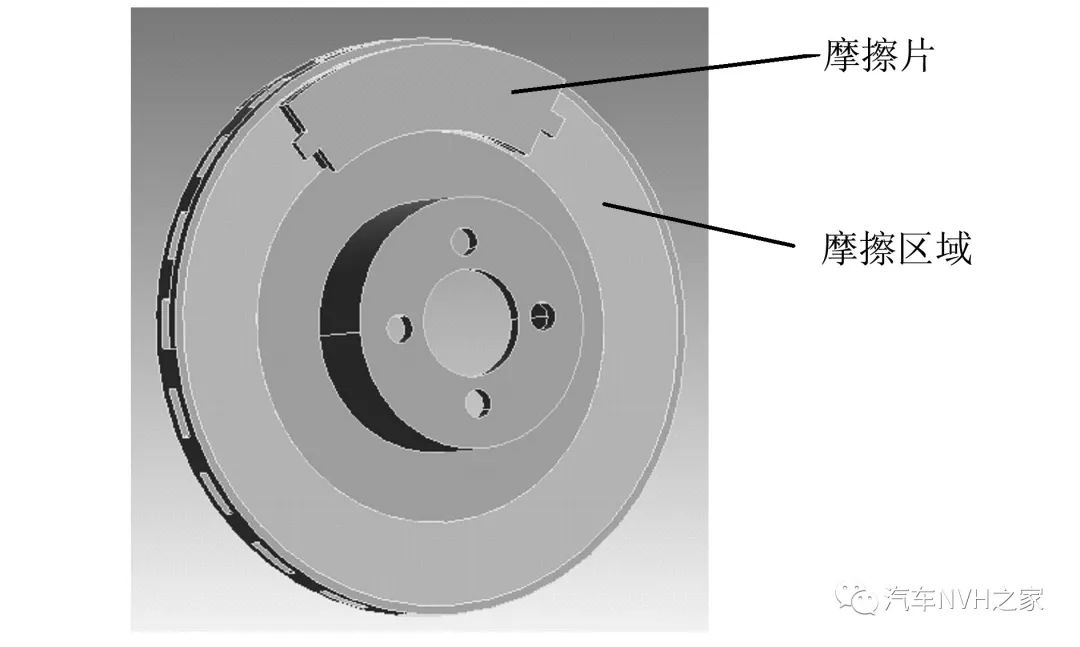
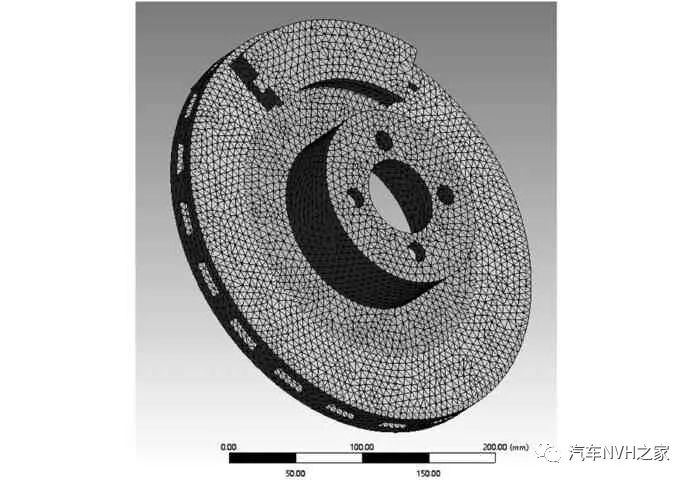
4 磨损状态下制动噪声的分析
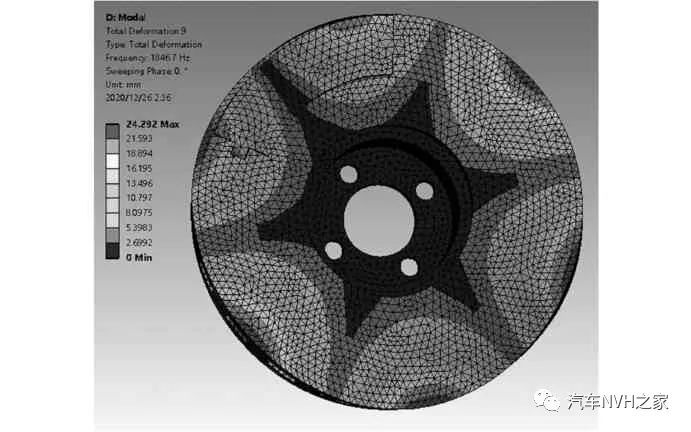
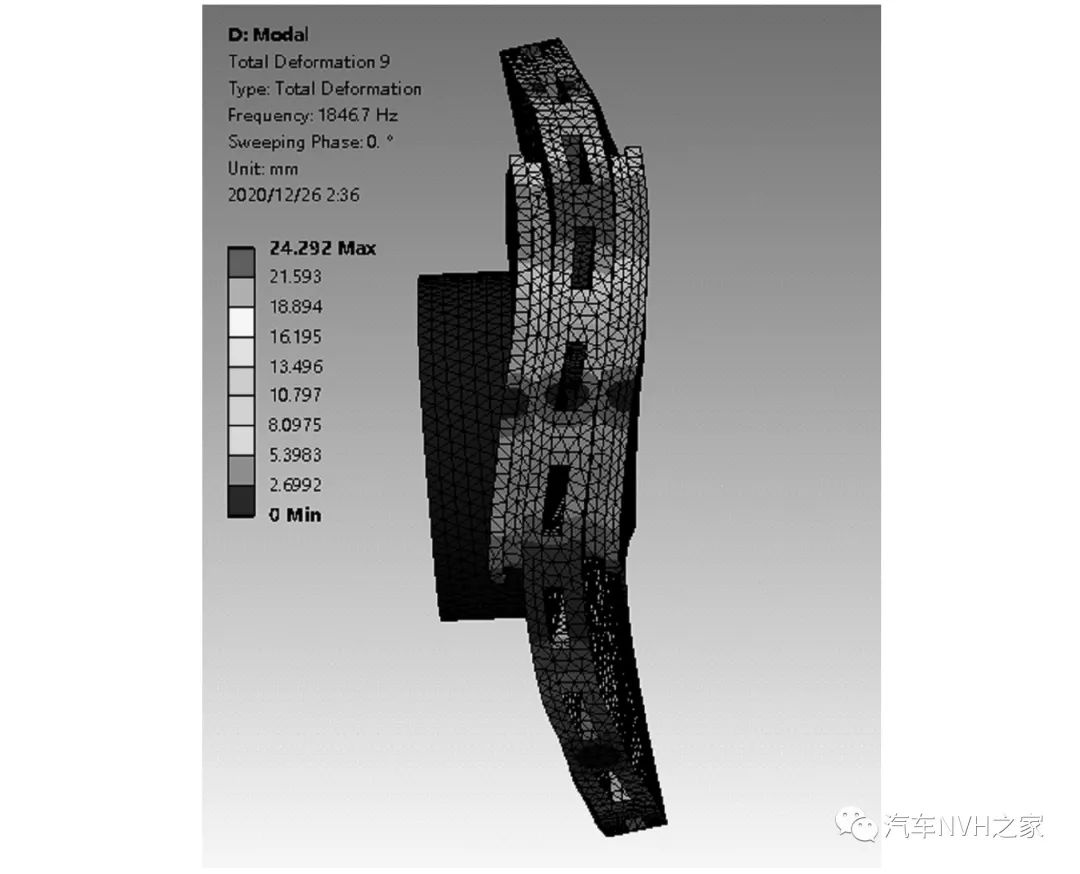
图7 制动器典型不稳定模态仿真图
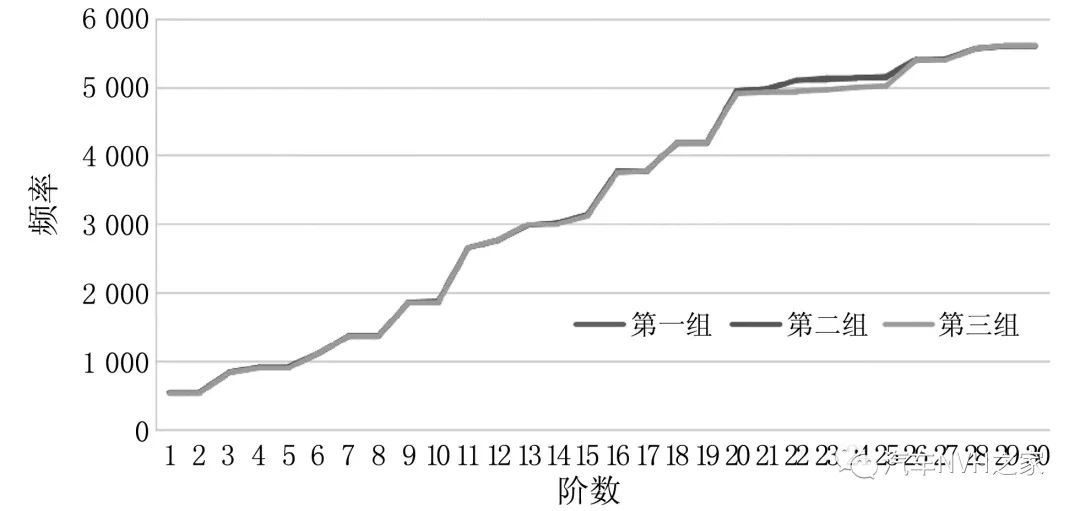
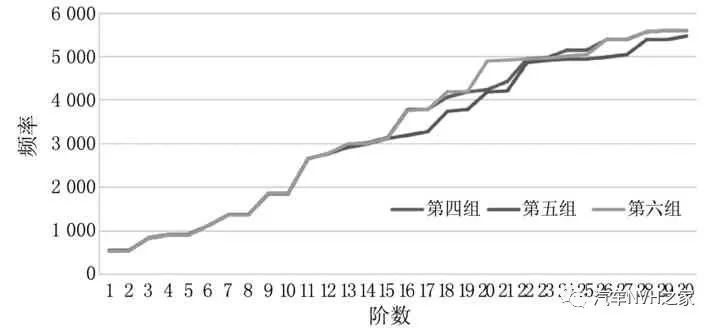
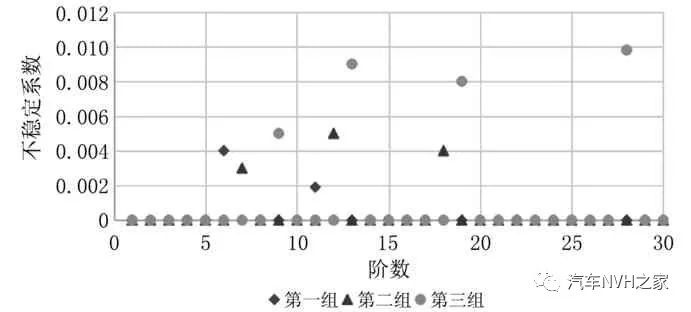
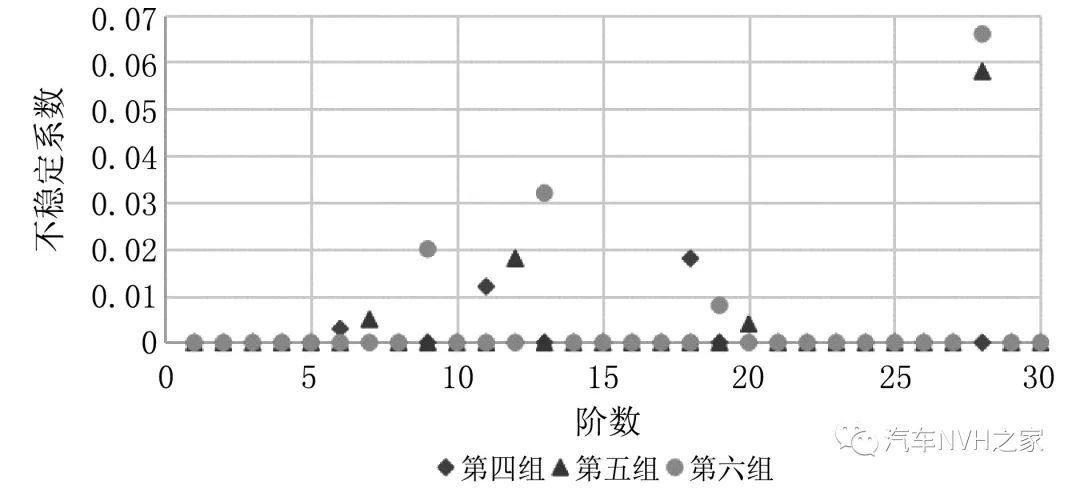
4.1 不同磨损状态下固有频率分布
4.2 不同磨损状态下模态不稳定系数的分布
4.3 仿真结果分析与制动器的优化改进
5 结论
作者:张雪松1,2, 王兆恒1
1.中原工学院 机电学院
2.郑州经贸学院 机械工程系
Previous:锐圆:浅谈摩托车创新的三个层面