信息中心
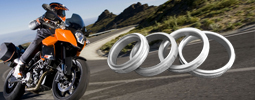
鼓式制动器、摩托车刹车圈、轮毂刹车圈专业生产厂家无锡九环2020年7月18日讯 针对某车型由于后制动鼓切向和纵向模态耦合导致的高频噪音问题,通过对制动鼓几何形状及尺寸的敏感度分析,探索其对制动鼓切向和纵向模态隔离的优化方向。首先建立了制动鼓ANSYS 有限元模型,并利用试验结果验证模型可靠性,然后通过DOE 试验矩阵分析方法,得出制动鼓主要几何参数与模态隔离的敏感度关系,最后通过试验对模态隔离和参数敏感度分析结果进行验证。结果表明:基于敏感度分析结果,通过优化制动鼓的关键影响因子,可以有效地提高制动鼓的模态隔离结果。
前言
在汽车制动系统中,制动噪音因响度大、发生频率高、机理复杂、控制难而成为该行业的研究热点。制动噪音的频率范围较大,一般在1000~16000Hz[1-2]。制动鼓是鼓式制动器的关键安全部件,是制动系统中最主要的噪音辐射体,其结构振动模态特性是制动噪声水平的关键决定因素,会影响整车的安全性、舒适性、操纵稳定性等基本性能。制动鼓的结构模态优化是解决制动噪音的一种有效途径[3-6]。模态特性包括固有频率、阻尼和模态振型,频率和振型是结构系统承受动态载荷结构设计时的重要参数,这些动力学参数可通过有限元模态分析和试验模态分析来得到。本文以某轿车的后制动鼓为研究对象,基于有限元模态分析方法,通过改变制动鼓几何尺寸参数来优化制动鼓切向和纵向模态,并探索制动鼓几何参数与其模态频率的敏感度关系,最后,通过试验模态分析结果对有限元模态分析结果进行验证,这对优化制动鼓结构设计及缩短设计周期提供了一定的参考,有效缩短设计过程并节省试制和试验成本。
1 制动鼓参数化模型建立
利用UG 软件建立制动鼓3D 实体模型,然后利用单元划分软件进行网格划分,将划分好网格的有限元模型导入ANSYS 中进行结构模态分析。图1(a)为所分析制动鼓实物,图1(b)为制动鼓的3D 几何模型,图1(c)为制动鼓有限元网格划分图。制动鼓参数定义如图2 所示,相应参数值如表1 所示,制动鼓的材料属性如表2 所示。有限元模型的单元类型为Hex 8 Solid 单元,Hex 8 Solid 单元是一个3D实体结构单元,网格平均长度为3mm,网格数量共36566 个,共47173 个节点。
2 制动鼓参数化模型可靠性分析
制动鼓自身有多阶共振频率,从而组成一系列离散的频率谱,即模态是一个频谱,是由物体的各阶共振频率组成的。随着振动频率的升高,振幅随之减小,影响也有所减小[9]。因此模态分析中前几阶的模态特性最为重要。而且,制动噪音频率范围一般在1000~16000Hz,因此通过ANSYS 进行模态分析时提取前 10 阶径向(ND)及前3 阶切向(T)模态频率,满足涵盖关注频率范围的需求。将该模型的模态分析结果与该制动鼓实物的模态试验结果进行对比,结果如表3所示。从表3 可以看出,该参数化有限元模型所计算出的前10 阶径向模态及前3 阶切向模态频率与制动鼓实物模态试验频率的相对误差均小于1%,最大误差仅为0.88%,因此,可认为所建立有限元模型具有较高可靠性和有效性。表4 为该有限元模型的各阶切向模态与各阶径向模态之频率差值|fND-fT|,可以看出该模型能够将切向模态与径向模态隔离至200Hz 以上,最小的模态隔离发生在6ND 与1T 以及8ND 与2T 之间,分别为241Hz 和223.9Hz,可以有效地避免产生频率共振。表3 制动鼓参数化模型模态分析结果与原始频率之比较
3 制动鼓参数敏感度分析
3.1 制动鼓参数敏感度的确定
实际零件开发过程中,制动鼓的内径DB 和安装面厚度TC 在设计阶段就已经是确定的值,一般不可变更。因此在制动鼓模型中,选择表1 中除了DB 和TC 外的11 个几何尺寸参数作为输入变量,将分析结果1T~3T、2ND~11ND 共13个模态频率作为输出变量。研究制动鼓模态特性对几何特征参数的敏感度,共可获得143 组敏感度值。定义某一输出变量F 相对于输入变量Xi 的敏感度为:若输出变量为正值,则说明该模态频率与该几何参数成正相关;若输出变量为负值,则说明该模态频率与该几何参数为负相关。图3(a)为1T 切向模态频率相对于11 个输入变量在-1%~+1%范围内变化时的敏感度分析结果。从图3 可以看出,1T 切向模态敏感度与输入变量防水槽YJ、工作面宽度YW、帽盖厚度TT 和TX 成正相关,与剩余输入变量DA、XD、YE、XF、YH、θ、XK 成负相关。从下图可以看出当DA 从-1%~+1%变化时,即DA 变化量为4.928mm 时,模态频率变化仅为11.2Hz。而XD、YE、TT、TX 从-1%~+1%变化时,即他们的变化量分别为0.40mm、0.402mm、0.13mm、0.11mm 时,模态频率变化分别为14.5Hz、4Hz、3.7Hz、3.9Hz。由于XD、YE、TT、TX 的参数基准值相对于DA、YH、YW来说较小,如果各个参数变化量都为1mm 时,相应的敏感度分析结果如图3(b)所示,可以看出1T 切向模态与各个参数的敏感度从大到小依次为XD>TX>TT>YE>XK>YH>YW>YJ>θ>DA>XF。表5 为制动鼓模型中各个输入变量分别增加1%时,1T~3T、2ND~11ND 共13 个模态输出变量的增减量。综合表5、图3(b)以及实际几何尺寸变化可行性可以看出,制动鼓的模态频率对制动鼓几何特征参数XF、YJ、YH、YW、θ及XK 的敏感度很小,即这几个参数值对制动鼓的模态频率影响相对较小。而制动鼓的外径DA,帽盖厚度TT、TX 以及最大外圈加强筋XD、YE 对对各阶模态频率的影响较大,尤其是能够将6ND 与1T 及8ND 与2T 的模态隔离得更好。而且,DA、XD 对6ND 与1T 的模态影响是相反的。因此,可以通过优化这几个参数将6ND 与1T 之间的模态隔离更大。在实际工作中,可以根据各阶模态隔离的需求,对某一设计参数或某些组合设计参数进行优化来达到隔离模态的目的。例如:当帽盖厚度TX增加0.5mm时,2T模态增加9.13Hz,而8ND 模态增加178.9Hz,因而8ND 与2T 的模态隔离从最初的223.9Hz 增加至393.67Hz。当帽盖厚度TX 增加0.5mm同时使制动鼓外径DA 减小2.46mm,可以使得8ND 与2T的模态隔离从原来的223.9Hz 增加到456.19Hz,而6ND 与1T 的模态隔离从241Hz 增加至311.46Hz。Note:
1.表中数据为设计变量增加1%时,反应变量的增减量。
2.表中括号内数值为制动鼓参数基准值。
3.2 制动鼓参数敏感度的验证
正为验证制动鼓参数敏感度分析的可靠性,将制动鼓特征参数YE 和DA 分别按照如下进行机加:#1 号制动鼓YE减小1%(0.2mm),#2 号制动鼓YE 减小1%(0.2mm),同时DA 减小0.81%(2mm)。记录机加之前及机加之后制动鼓各阶模态,同时,将制动鼓的实测材料密度及弹性模量代入制动鼓参数化模型中进行修正,可得到修正后制动鼓模态频率的理论差异。#1 号制动鼓的分析结果如表6 和图4 所示,#2 号制动鼓的分析结果如表7 和图5 所示。从表6 和图4 可以看出,随着1#制动鼓YE 尺寸的减小,各阶ND 模态的实测值与理论值都呈减小趋势,且ND 模态的实测差异与理论差异较为接近。而1T 实测模态同1T 理论模态呈变大趋势,2T 与3T 的实测模态与理论模态呈减小趋势,但2T 与3T 的实测模态差异比理论计算差异稍微偏大一些,最大差异都在0.58%以内。而且,从表6 分析可以看出6ND 与1T 的模态隔离从216Hz 增加至236Hz,而8ND 与2T 的模态隔离从原来的253Hz 增加到309Hz。从表7 和图5 可以看出,当同时减小2#制动鼓的YE 和DA 尺寸时,各阶ND 模态及T 模态的实测值与理论值都呈现减小趋势,且整体模态的实测差异与理论差异的较为接近。而且,从表7 数据可以看出6ND 与1T 的模态隔离从253Hz增加至298Hz,而8ND 与2T 的模态隔离从原来的323Hz 增加到673Hz。基于上文分析可知,通过优化制动鼓的单一尺寸参数YE或者组合尺寸参数YE 和DA,可以有效地提高制动鼓的模态隔离结果,并说明该制动鼓参数化模型的敏感度分析具有较高可靠性。
4 结论
(1)利用ANSYS 对制动鼓进行参数化建模并对其模态进行试验验证,模态频率误差均小于1%,改参数化模型可靠性较好。(2) 通过对制动鼓模态与设计参数之间的敏感度研究,识别影响制动鼓模态隔离的关键因子:制动鼓的外径、帽盖厚度和最大外圈加强筋厚度。(3)基于参数敏感度分析结果,通过对关键因子进行优化分析,可快速解决制动鼓的模态隔离问题,有效缩短设计周期。